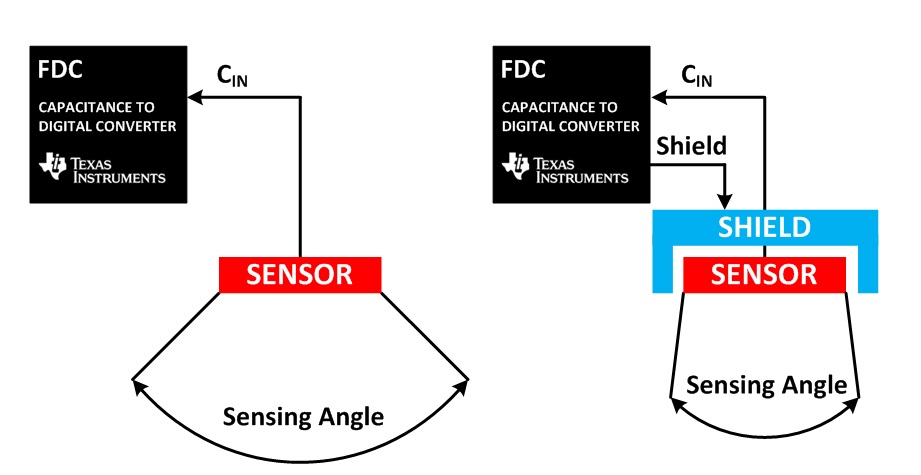
Driven Shield Capacitive Sensor. Capacitive sensing method is detecting the change of capacitance on the sensor due to users touch or proximity. Login Sign up Search Expert Search. FDC1004 features active shield drivers which can reduce EMI interference and help focus the sensing field of a capacitive sensor. This adds significant cost and bulk when there are multiple sensors.
NASA used this driven-shield idea in a large-area capacitive sensor two decades ago. Most common types of conductive layers consist of solid or hatched planes in close proximity to the sensing. Moving the sensing circuitry local to the sensor itself whether you use a microcontroler or dedicated capacitive sensing IC costs less than even a. TOOLS RESOURCES Title. Using a driven shield requires use of a coaxial cable for each capacitive sensor and added electronics to drive each shield. Any external interference will couple the shield signal with minimal interaction with the sensor signal.
Precision Capacitive Sensors for Accurate Position Measurement Non-contact Position Measurement with High Resolution over Short Ranges.
For the Microchip solution a sensor can be any conductive material connected to a pin on a PIC MCU RightTouch or mTouch turnkey device. In case of PTC sensor measurement is sequential. This adds significant cost and bulk when there are multiple sensors. So Y0 and Y2 sensors in your design cannot be acquired in parallel. A conductive shield that is disposed near the sensor wherein a signal is driven on the shield that is similar to the signal induced on the sensor thereby reducing stray capacitances and protecting t. A capacitive proximity sensing 18 element backed by a reflector driven at the same voltage as and in phase with the sensor is used to reflect the field lines away from a grounded robot arm 16 towards an intruding object 20 thus dramatically increasing the sensors 18 range and sensitivity.